We’ve disassembled Geely Coolray engine
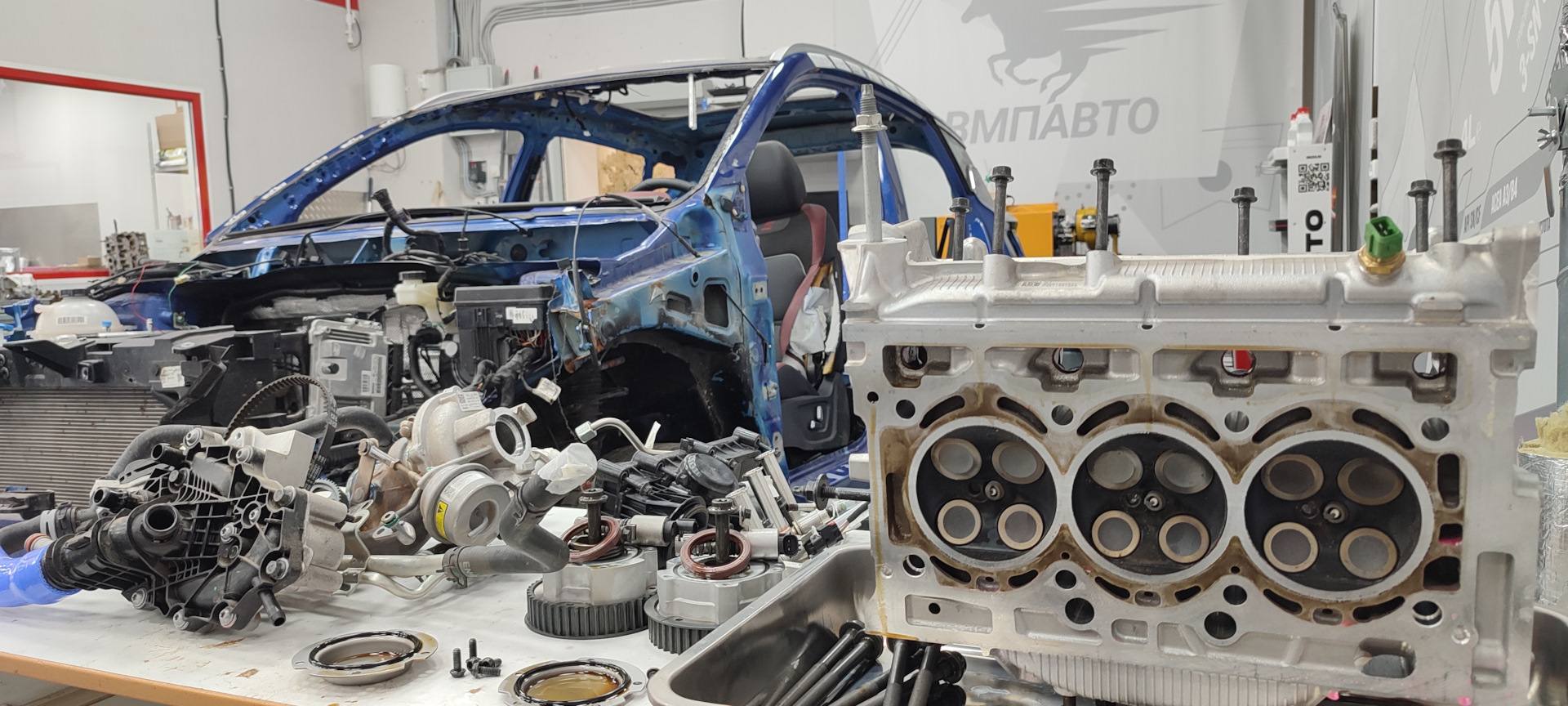
Friends! As you know, our company has the ability to conduct oil tests not only on laboratory equipment, but also on our own engine stands. Today we want to tell you about how it happens, on the example of testing new 0W-20 oil on SP package.
For testing of energy-saving oils we once purchased a Geely Solrau car. The car suffered a serious accident, but the three-cylinder turbocharged engine JLH-3G15TD and seven-speed robotized transmission remained absolutely intact. In addition, at the time of the accident the car had run only 1050 km. It became another engine test bench for us.
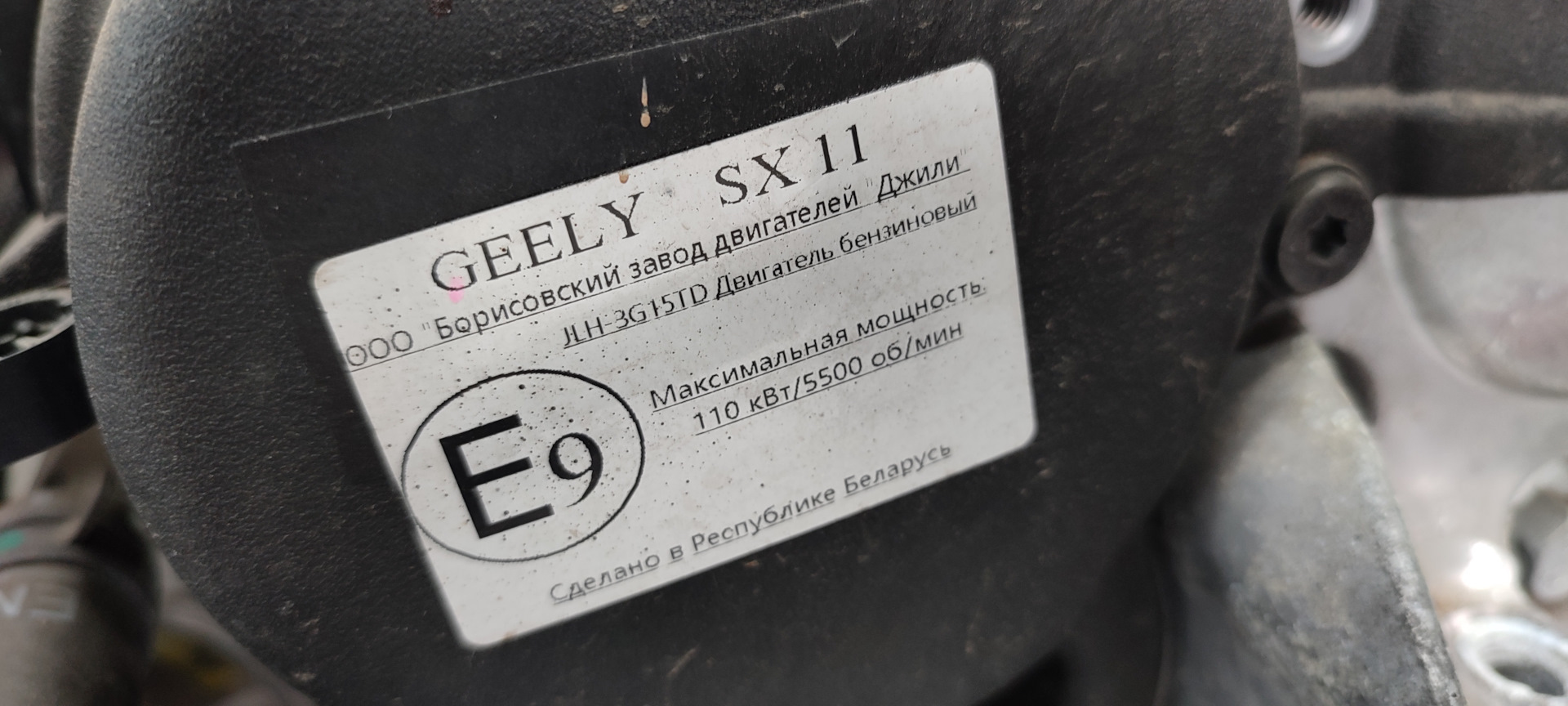
Everything that was mangled was removed from the car. As a result, the car was practically a bare hulk. Only the engine and gearbox, running gear, gas tank, instrument panel and driver’s seat were preserved. Electromagnetic retarders were installed instead of driving wheels.
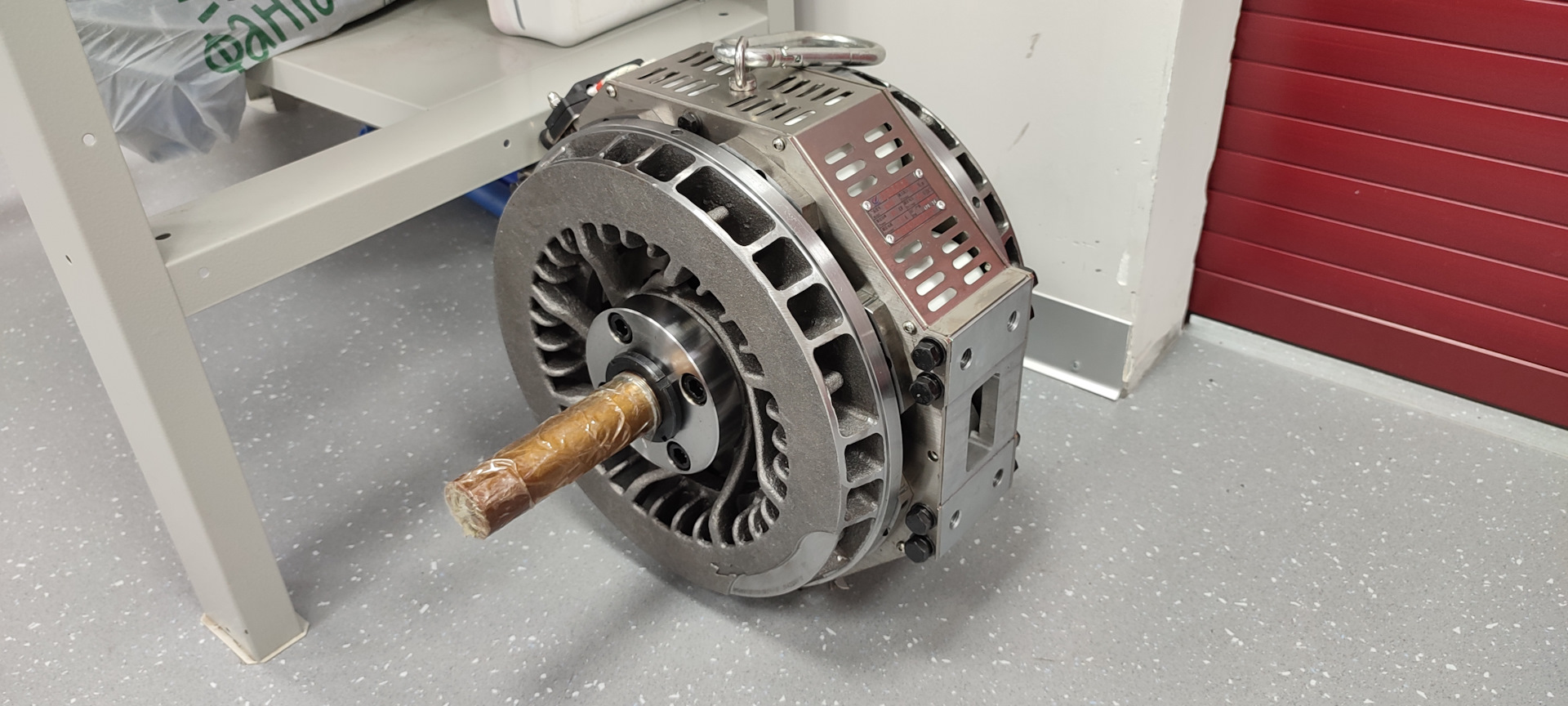
One of the retarders before installation on the stand.
In their normal life, these devices help the braking system of buses and trucks to slow down. In our case, retarders load the engine and gearbox, simulating the movement of the vehicle in different modes.
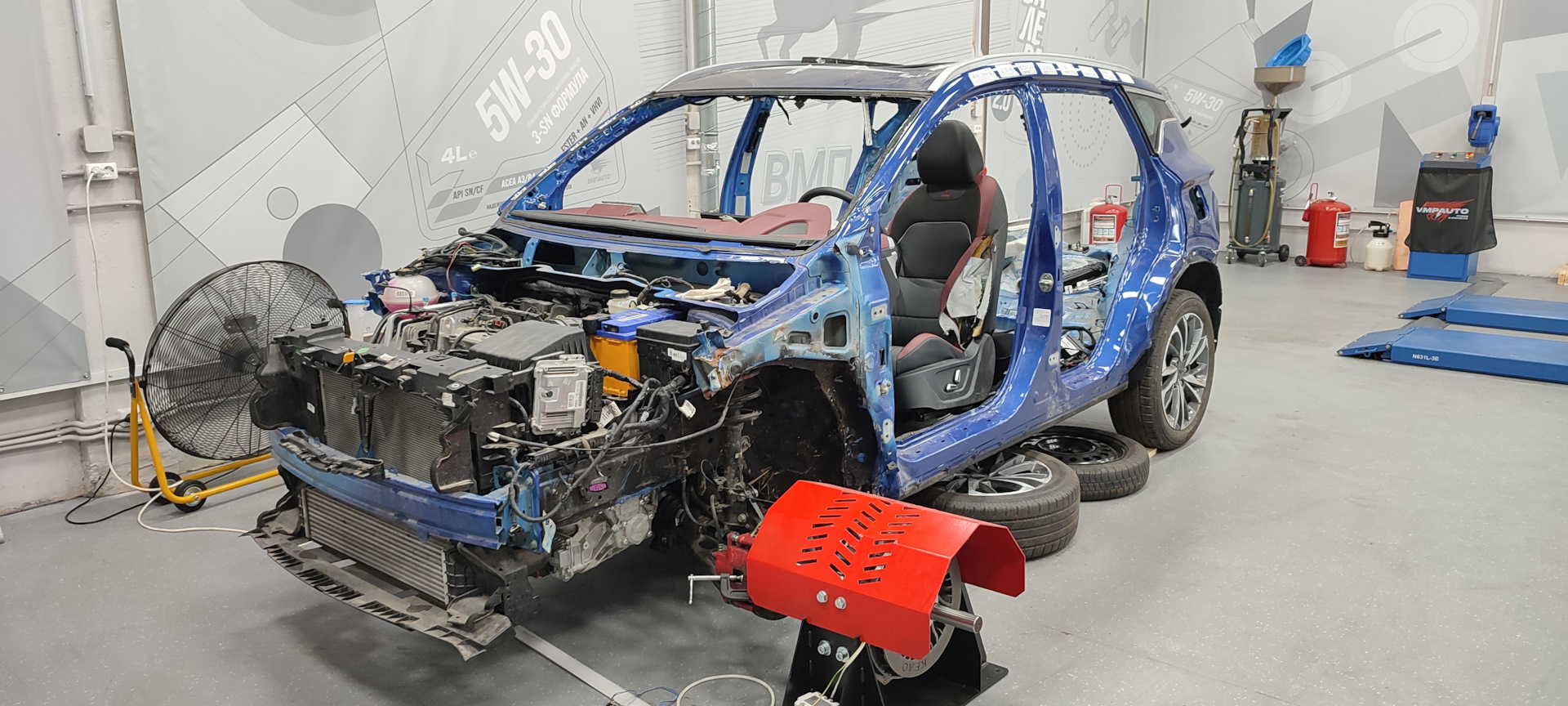
Retarders are attached to both drive axles.
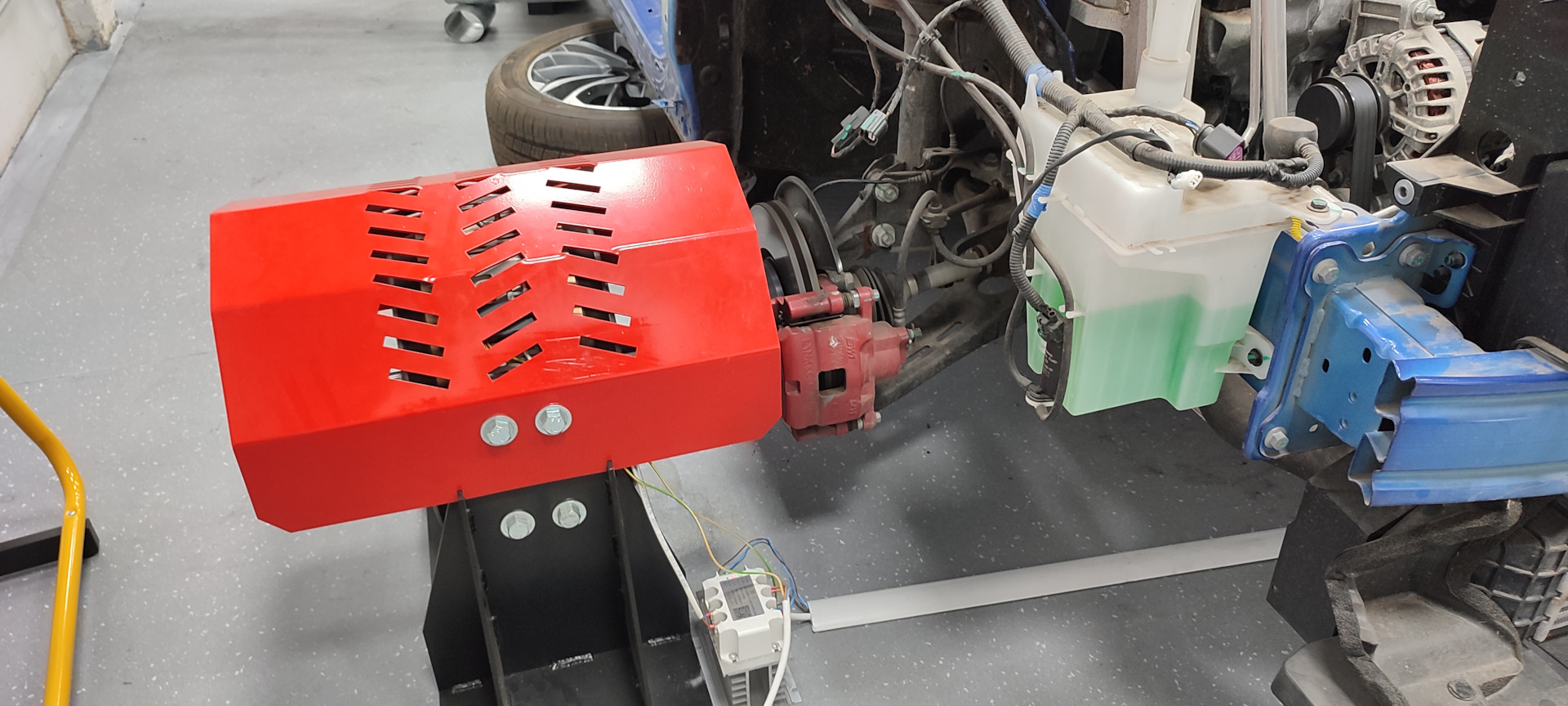
The retarder is attached to the wheel hub via specially milled flanges.
Initially, we planned to set “driving” modes using the standard cruise control. You can’t sit in the car all the time and not press the accelerator pedal. However, due to damage to various sensors, it refused to work. Then it was decided to create a mechanical cruise control. M6 stud, three nuts, a metal tube and a “stop” printed on a 3D printer allowed to solve the issue of long-term retention of engine speed at certain modes. By turning the tube like a potentiometer, we either pressed the accelerator pedal or released it.
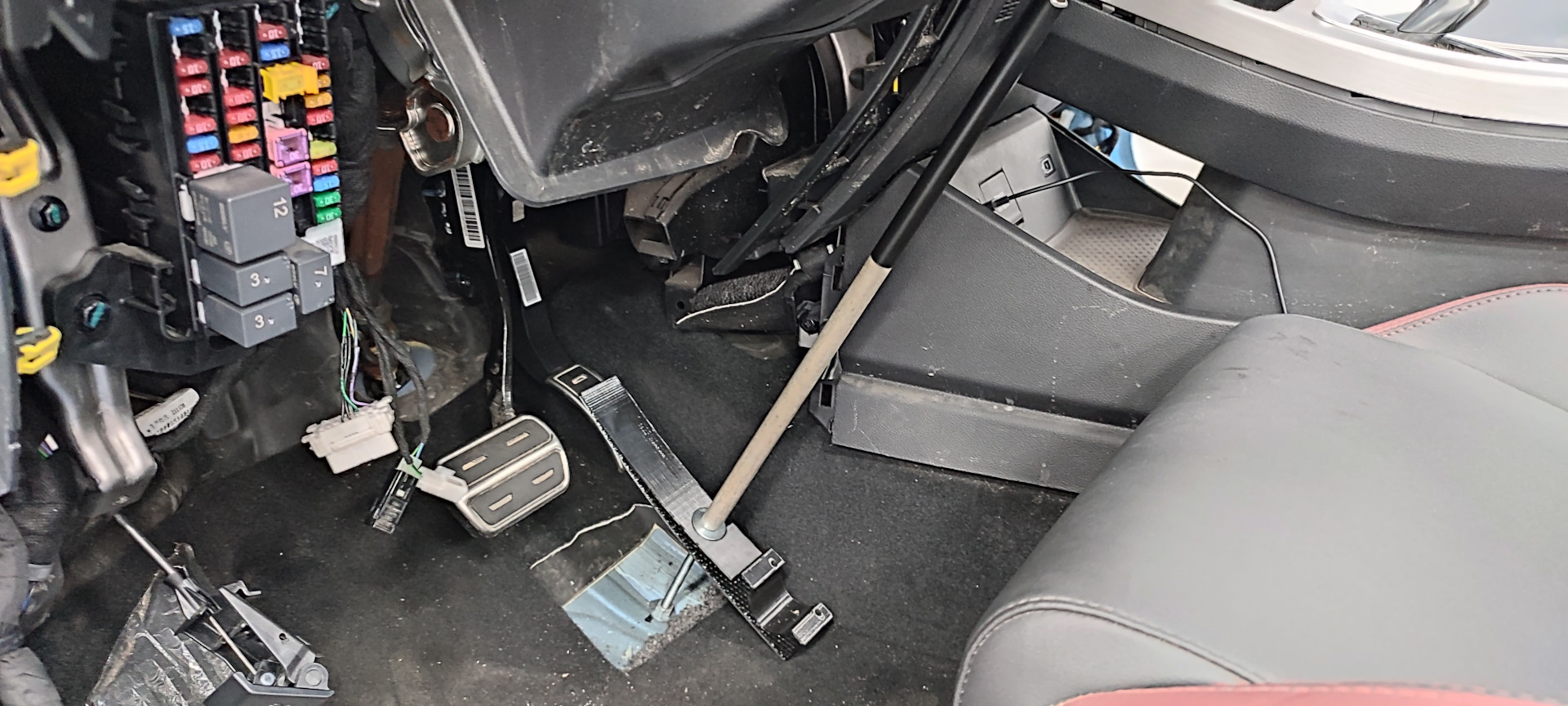
Improvised cruise control.
One of the many tests an oil must pass before it appears on store shelves is the high-temperature deposit test. According to ASTM, the engine is run in various modes for 90 hours during this test. Every 10 hours, an oil sample is taken for further testing and the oil level is measured. After the tests are completed, the engine is disassembled and the condition of the soot on the piston skirt is used to evaluate how well the oil resists high temperatures.
It should be noted that in this study, the soot and lacquer deposits are not evaluated in the combustion chamber, but below the first compression ring.
Before starting the tests, the engine was flushed of residual factory oil. After that its place in the crankcase was taken by our 0W-20 oil on SP package. The oil was poured exclusively by means of measuring utensils to make it easier to count its losses on carbon monoxide in the future. After completion of all preparatory works the engine was started. The mode was selected so that the oil temperature in the engine did not fall below + 108 ºC. Its maximum value should be + 120 ºC. The temperature, as well as many other indicators, was monitored using a connected scanner.
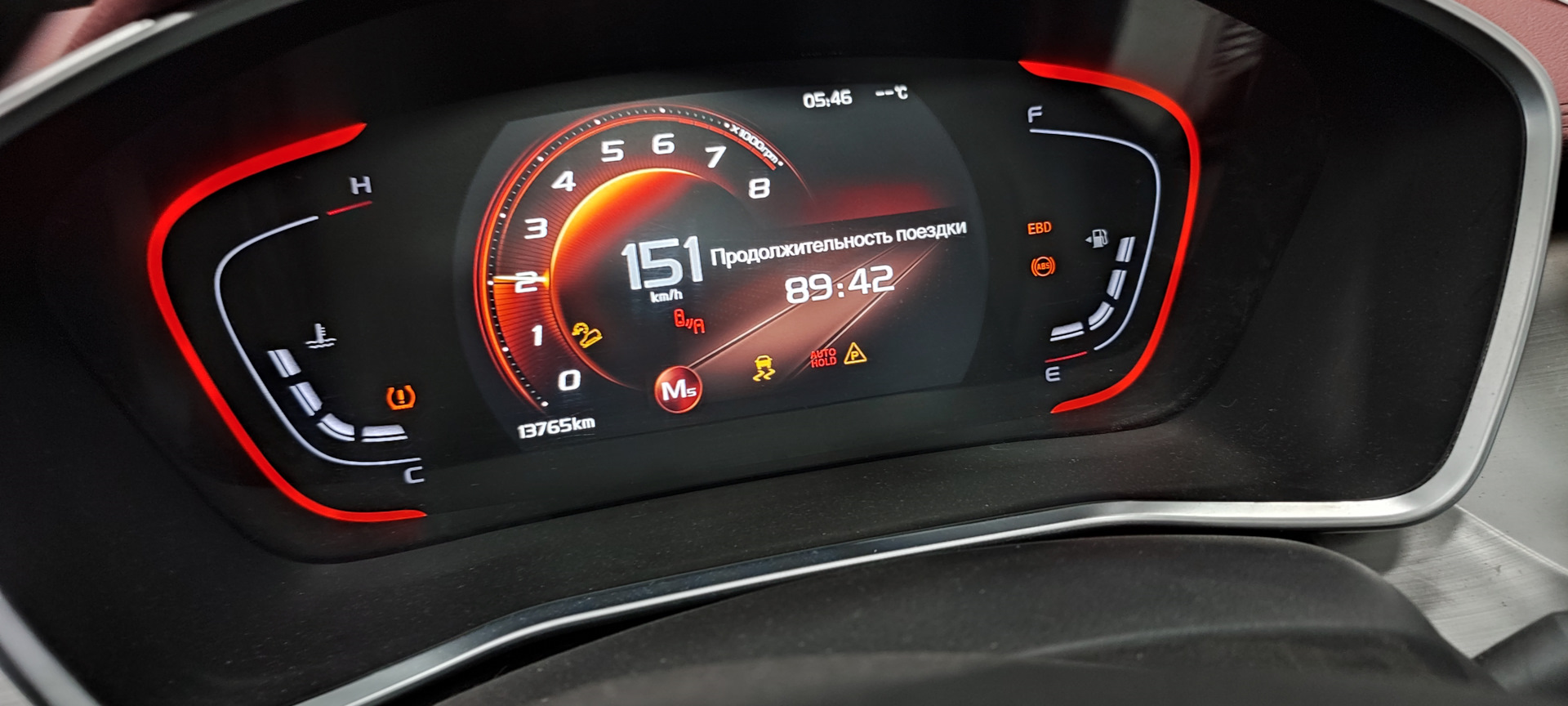
The speedometer was distorted due to the absence of some sensors. The tachometer and the hour meter showed the truth.
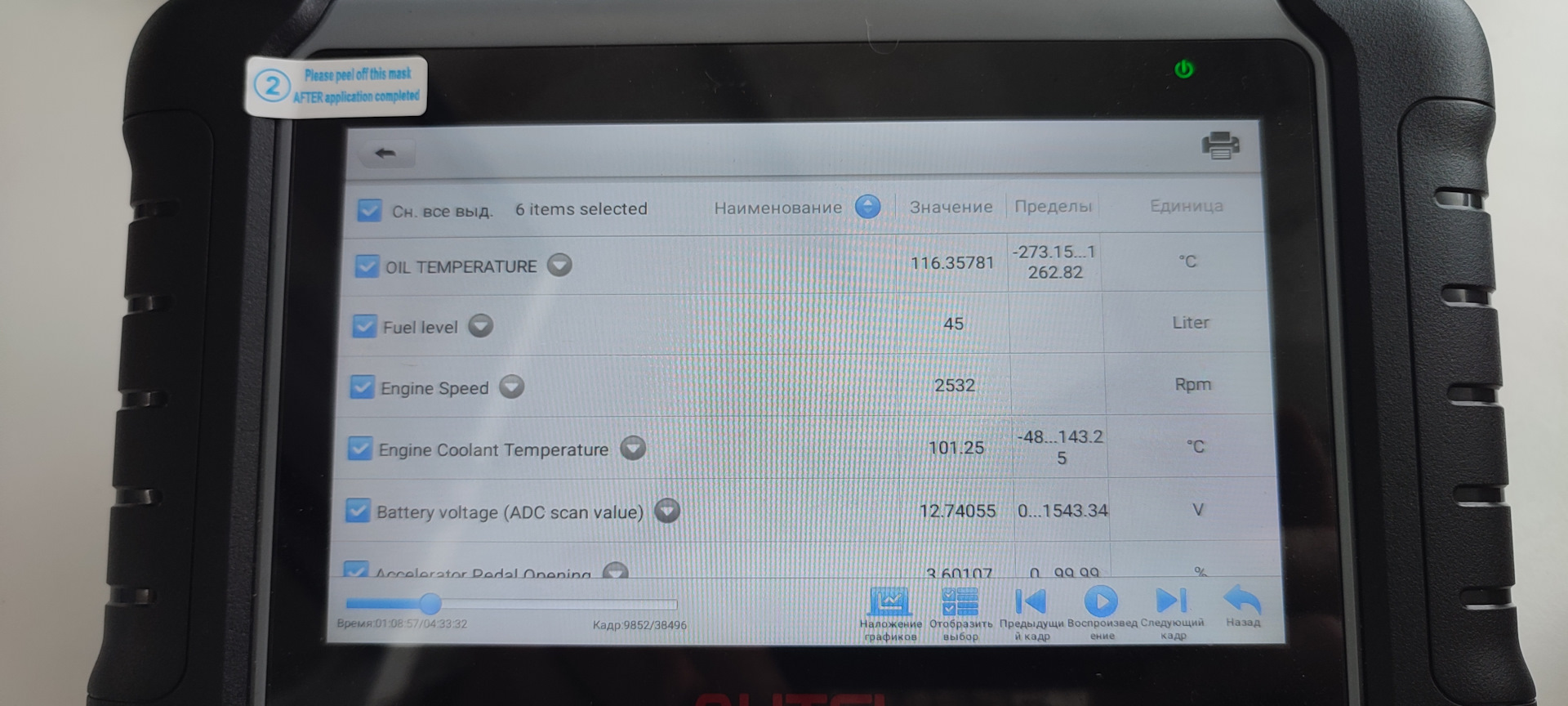
The missing data was read by the scanner. The scanner was also used to double-check the data given by the instrument panel.
We tried to keep the rpm around 2500-3000 rpm. They dropped only in transient modes. The load on the retarders was about 30%, provided that they could create a torque of 500 N.m. The temperature in the room where the engine was running was around + 30 ºC. Every 10 hours the engine was stopped for 10 minutes. The oil was sampled, its level was measured, the fuel in the tank was replenished and the bench was restarted. At the end of the fourth day it was decided to slightly change the test conditions and extend the engine running time up to 110 hours. Thus, we decided to equate engine hours to conditional kilometers of mileage. In this case, with all the errors it became about 10 000 km. As a result, the engine worked for almost five days.
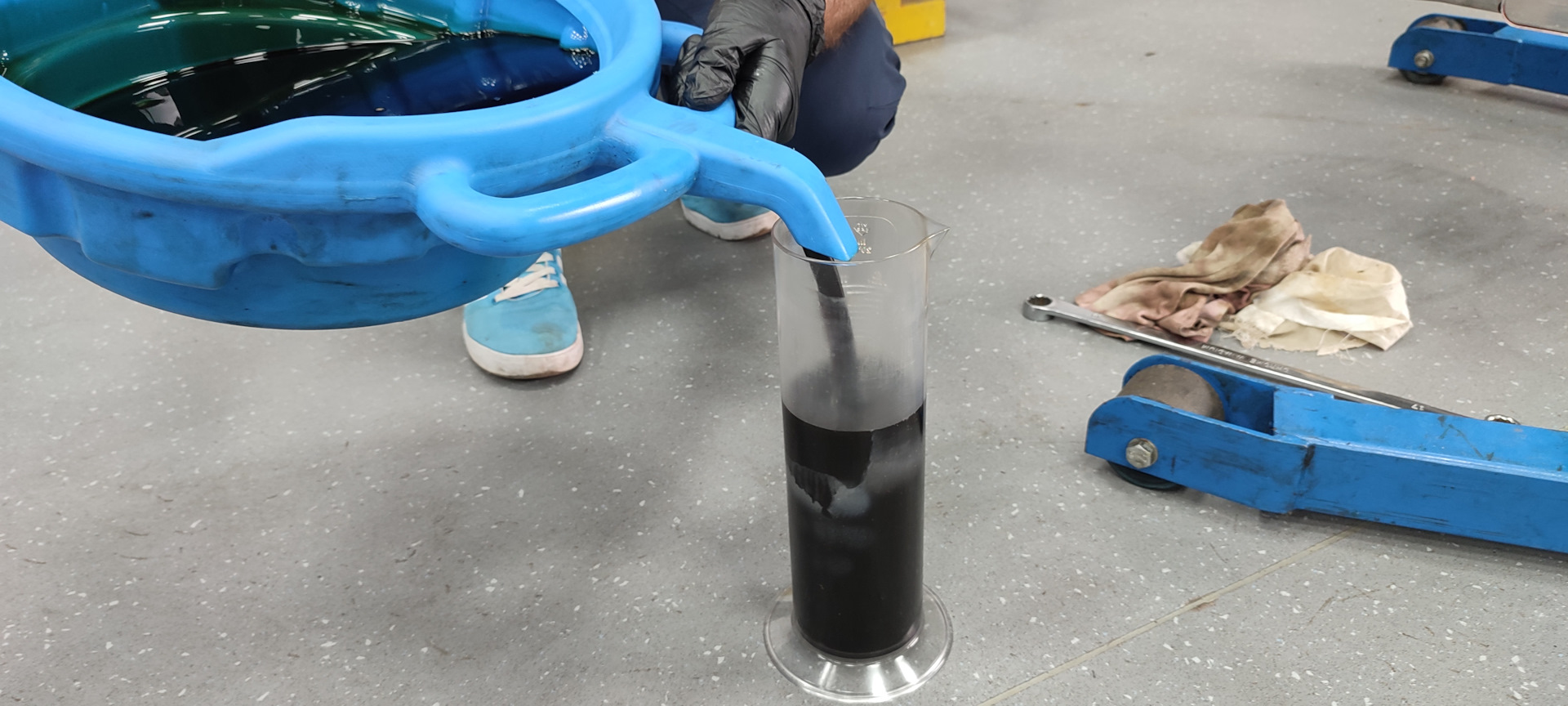
Oil was poured in and drained by means of measuring utensils.
After the end of the study, the oil was drained first of all. Taking into account sampling, the oil consumption per 10 000 km of mileage left 1 000 ml, which is a very good indicator for turbocharged engines. But to a greater extent, of course, we were interested in the condition of the engine. Already taken out of the engine compartment, the engine was disassembled in just a couple of hours.

Under the valve cover is perfectly clean.
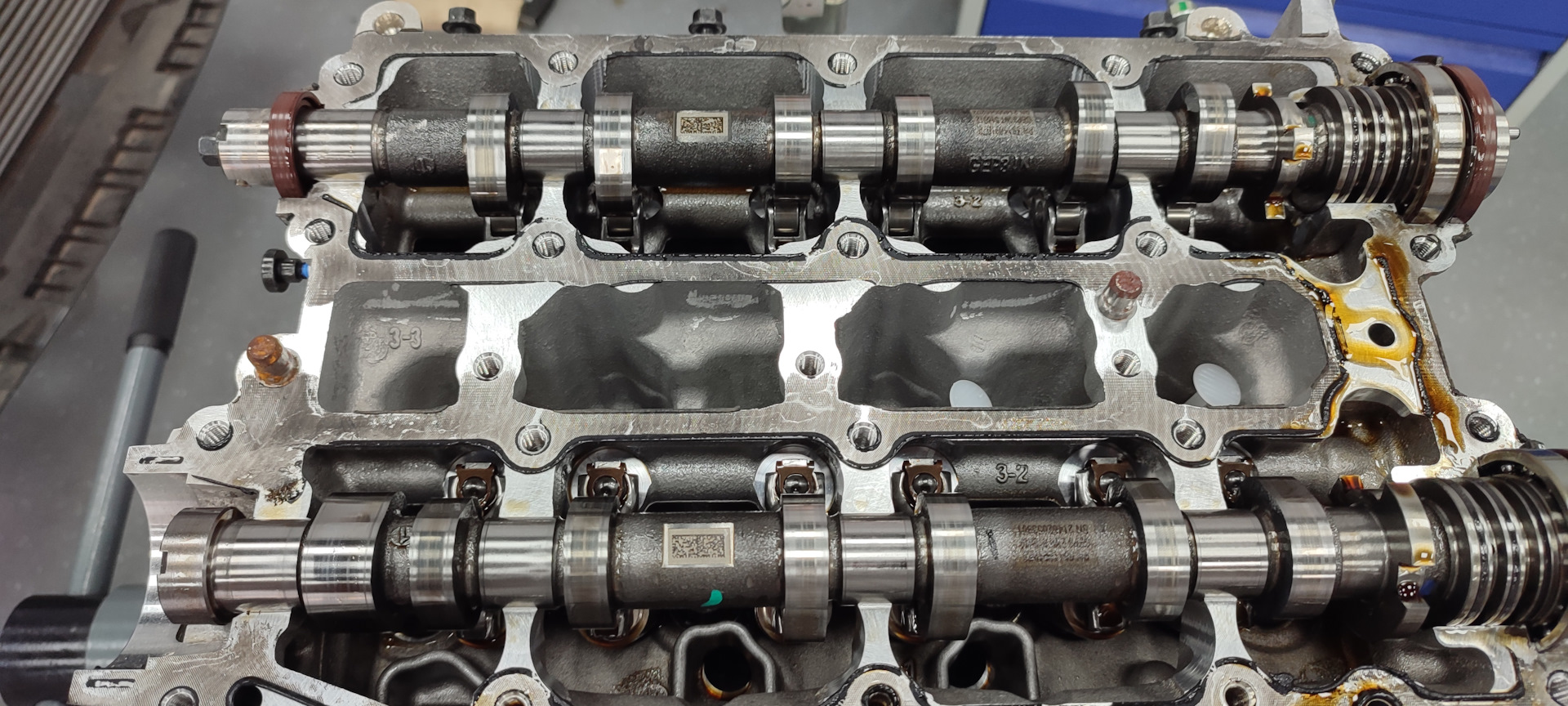
There is not even a hint of low temperature deposits.
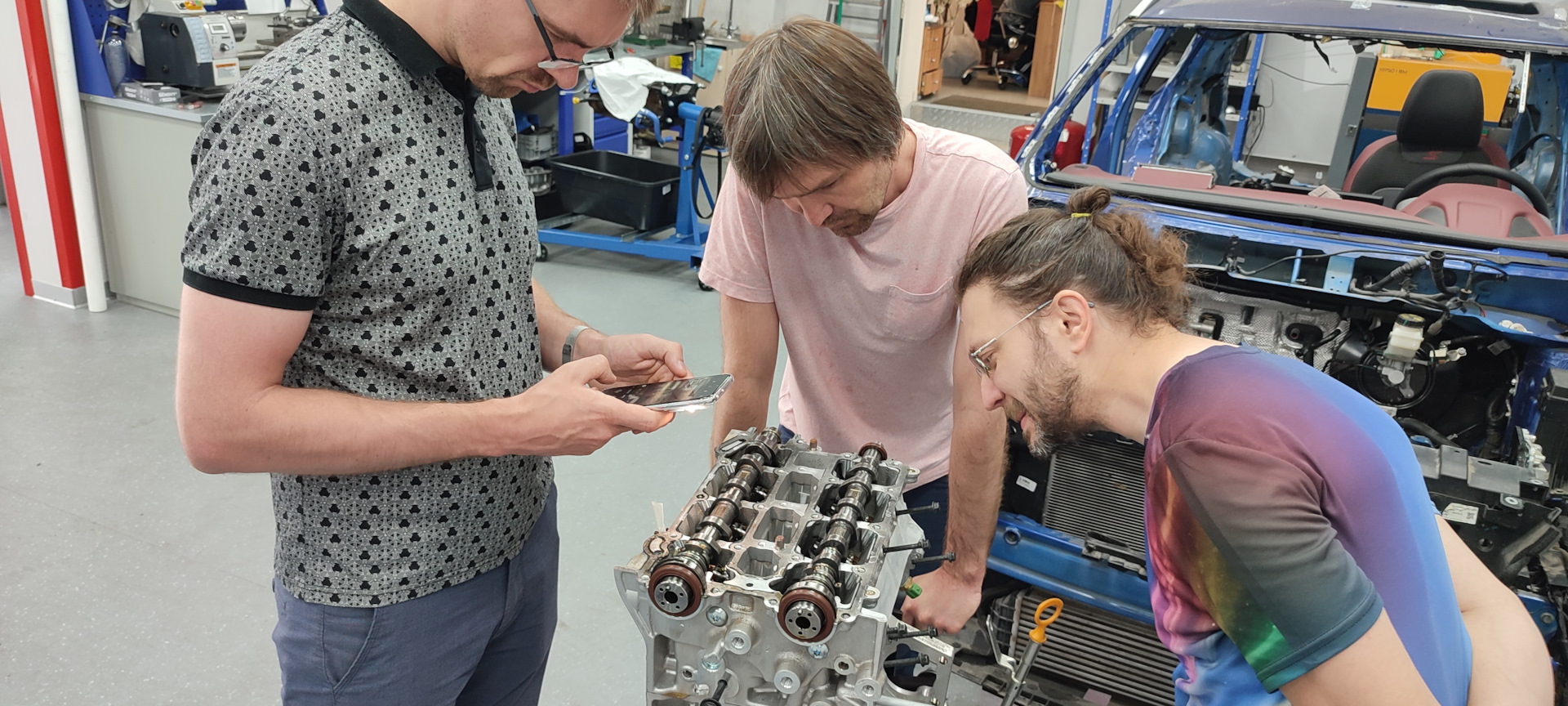
The inspection was done with six eyes. Each assembly or part was recorded on a photo.
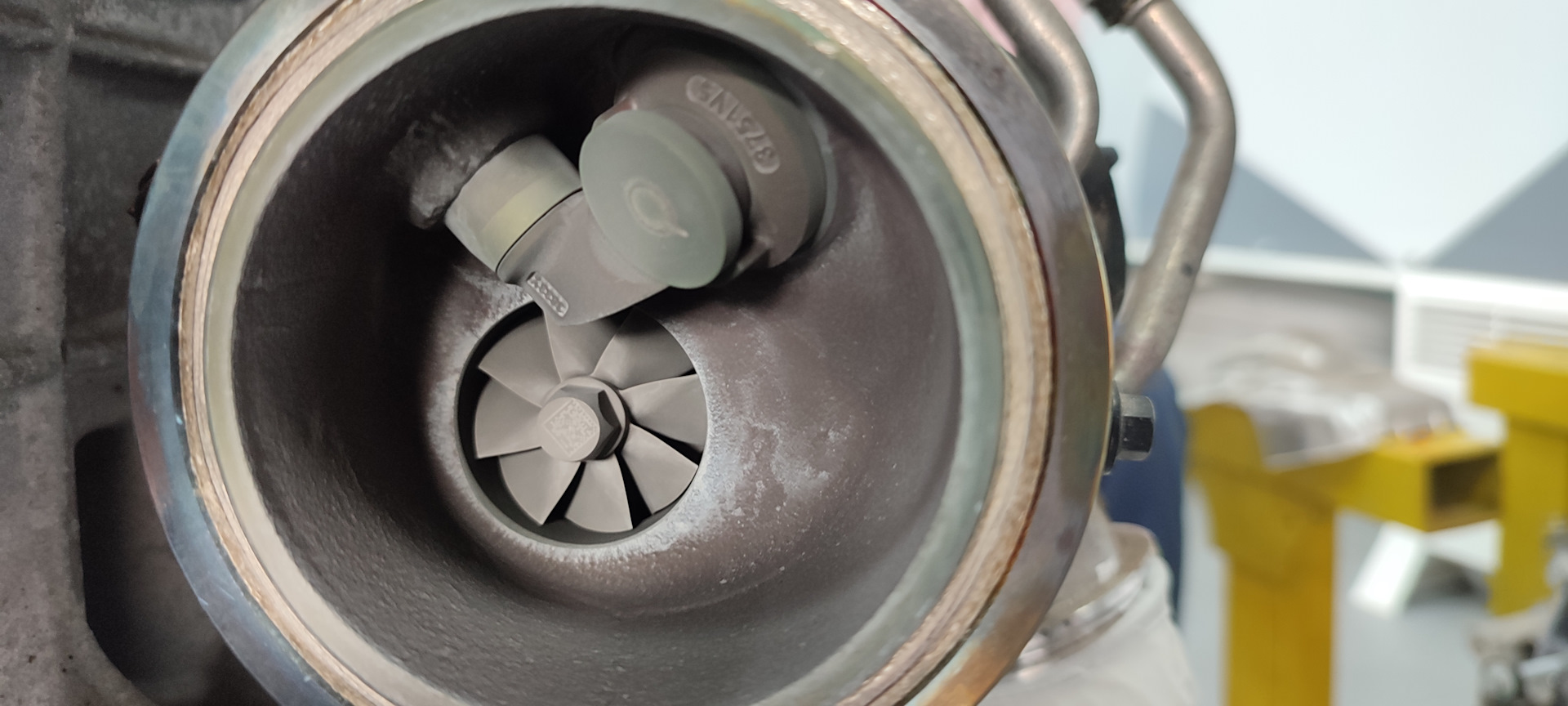
Dry turbine with no signs of fouling.
First of all, we evaluated the low-temperature deposits. No deposits were seen under the valve cover, as well as on other parts of the engine. The engine shone with pristine cleanliness. There was no hint of deposits even in the places where indelible residue normally accumulates after oil removal.
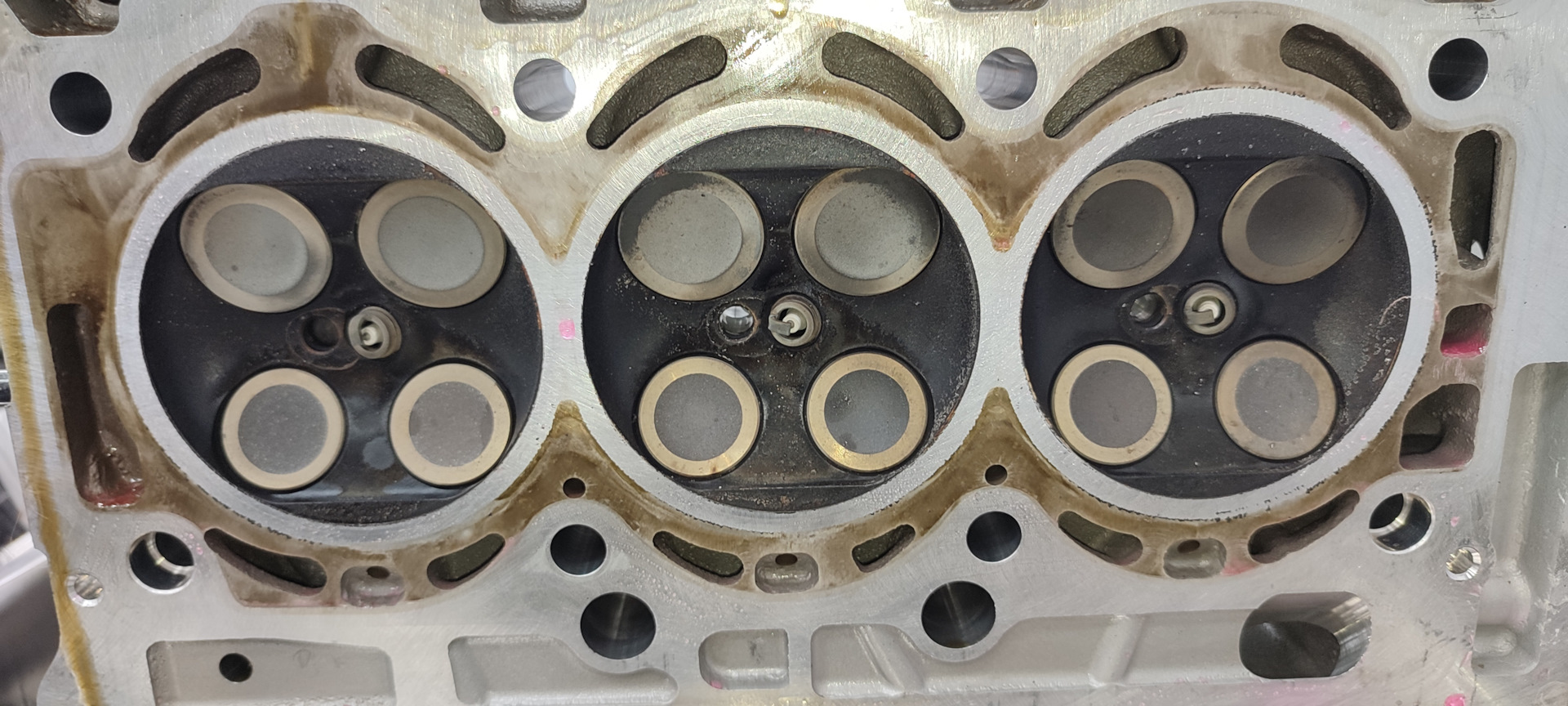
There is soot in the combustion chamber, but it is insignificant.
Next, the block head was dismantled. Of course, we did not see perfectly clean combustion chambers, but the amount of soot that was on their vaults and pistons could not be called critical. Moreover, this soot was literally wiped off with a finger.
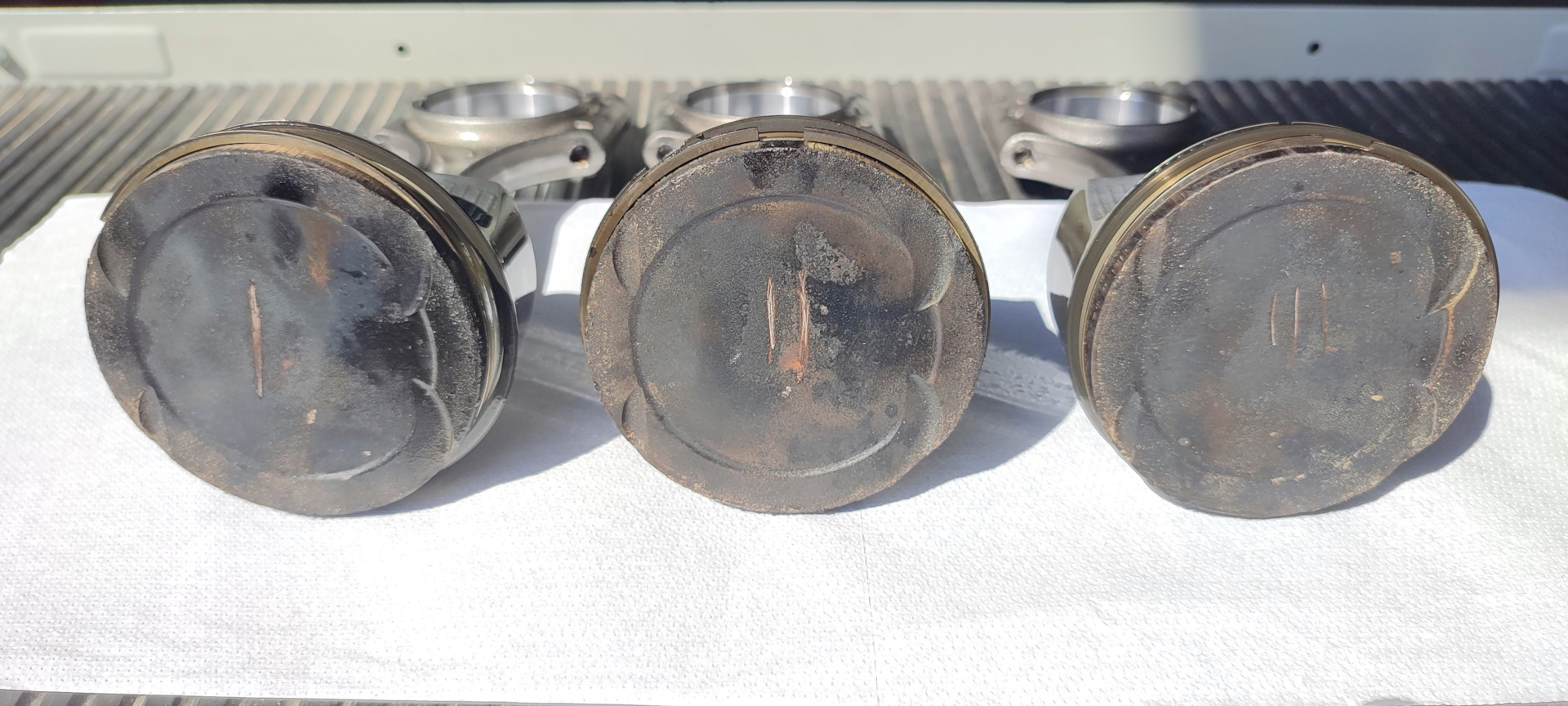
The pistons are slightly “sunburned”.

Piston skirts with no signs of any deposits.
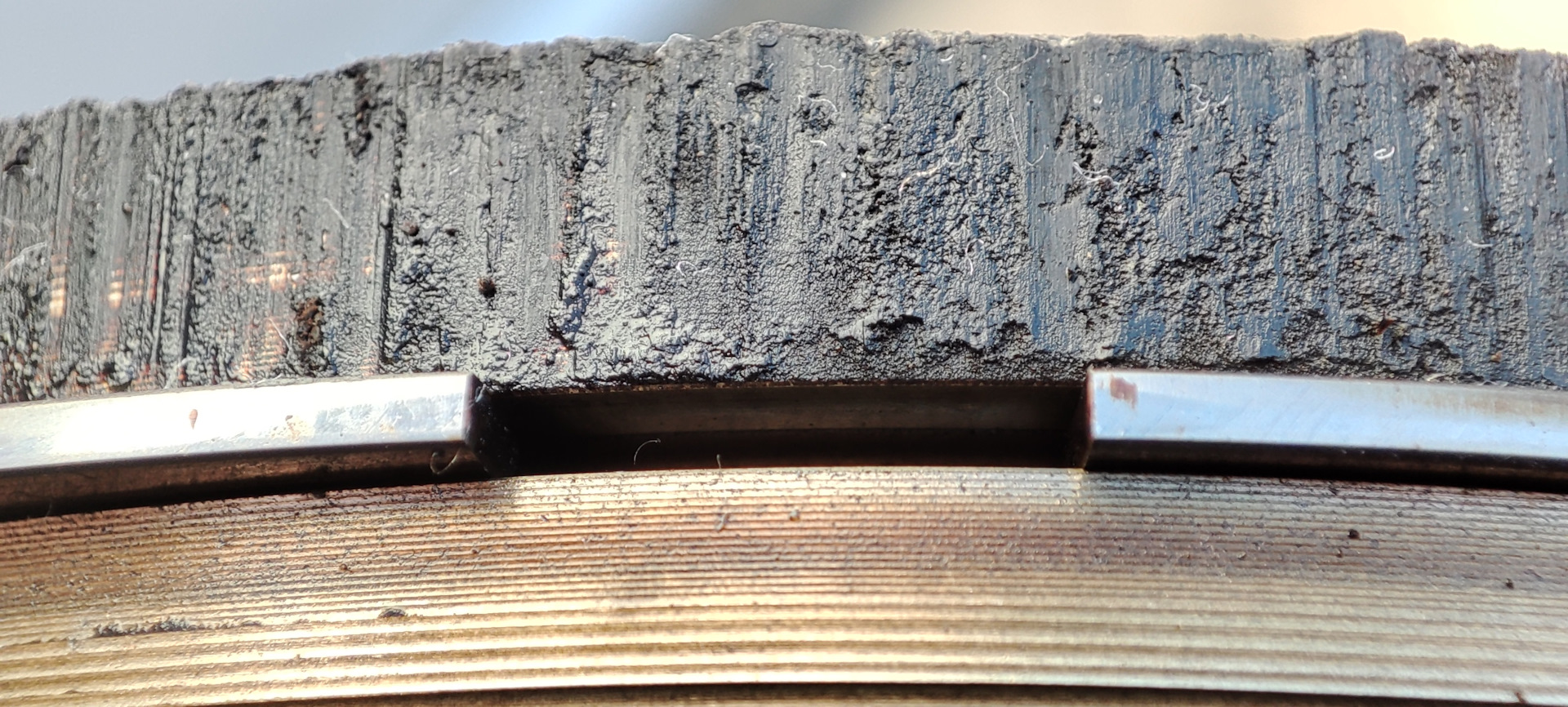
There is no soot below the first compression ring.
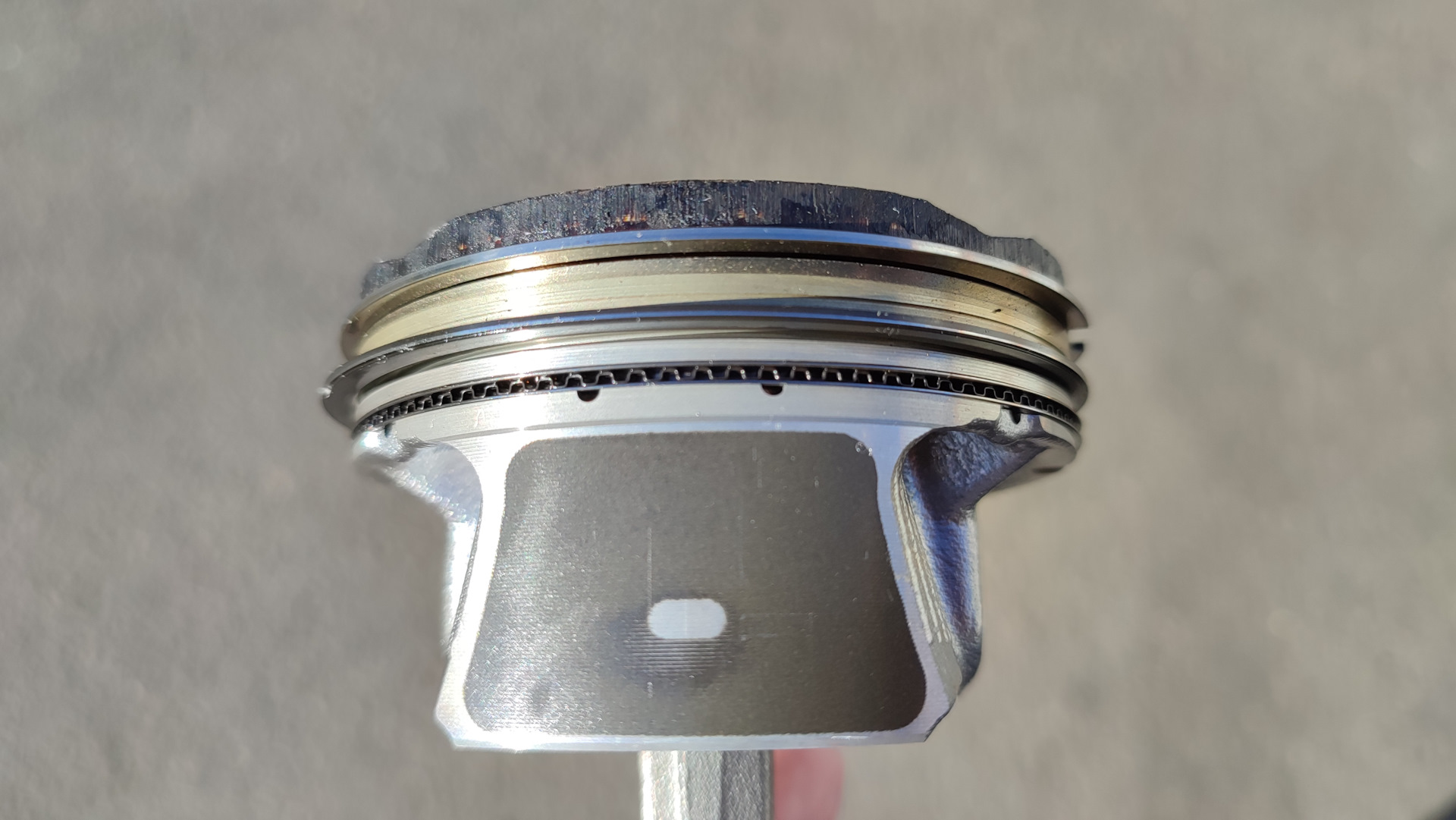
Piston skirt. Antifriction coating in place.
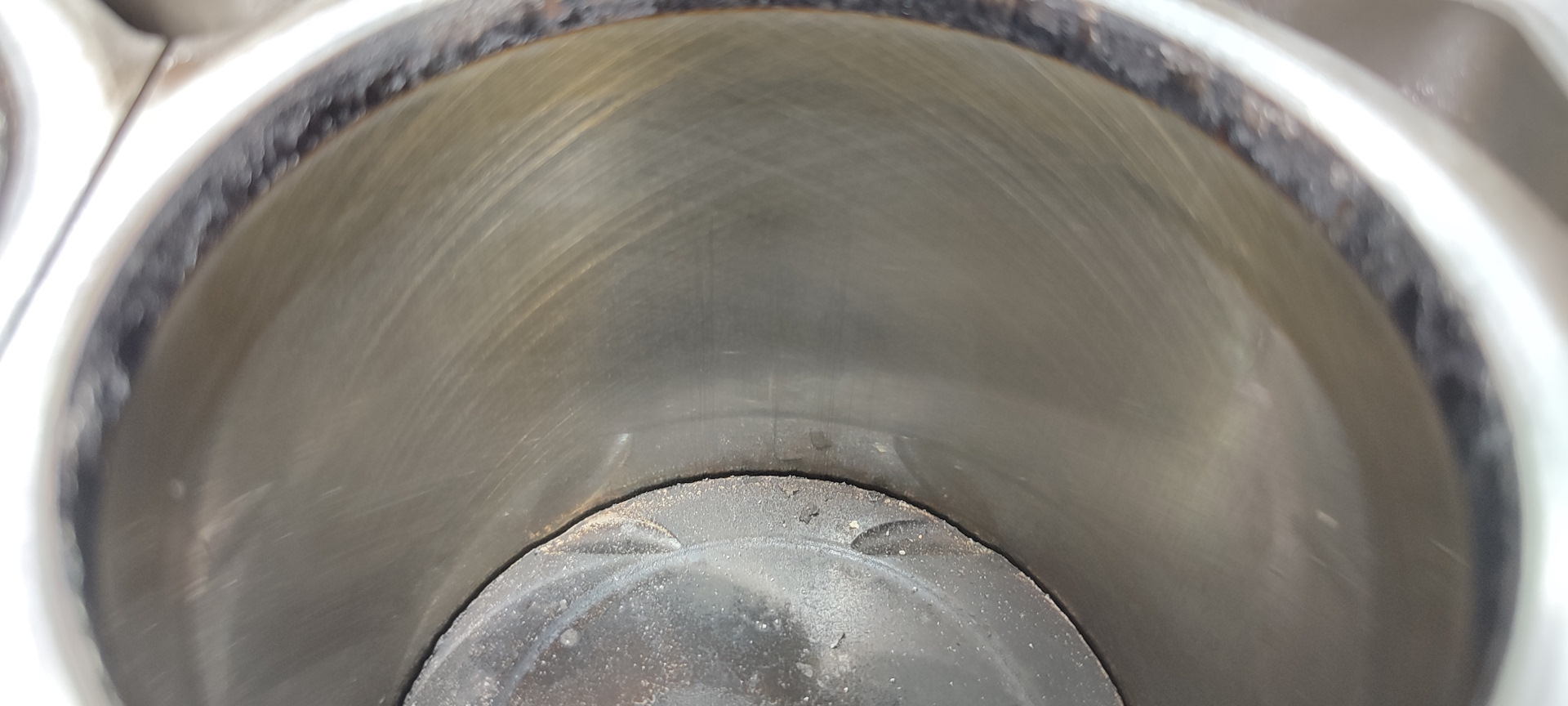
Condition of cylinder walls.
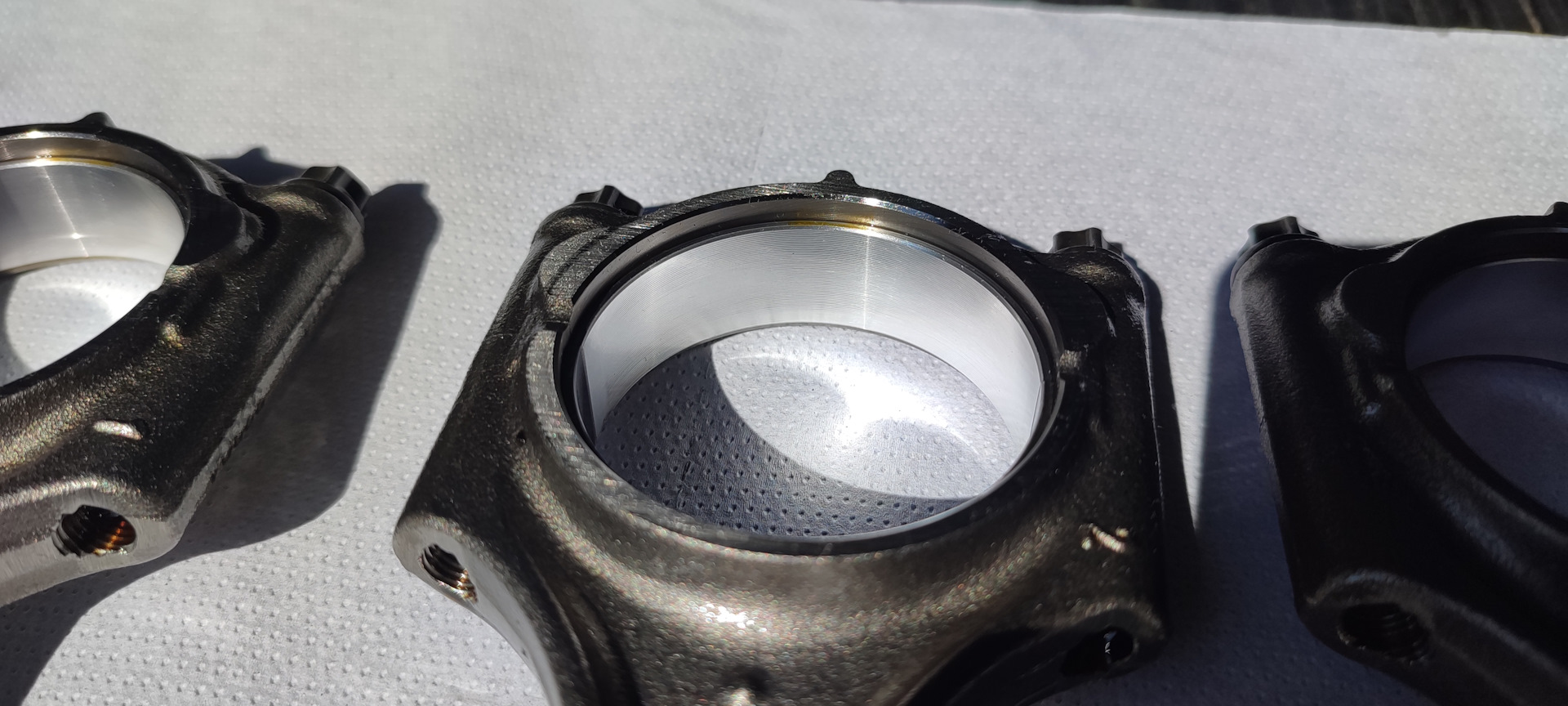
Crank liners with no signs of wear. The absence of wear was confirmed later by elemental analysis. Iron particles as well as other metals in the samples are 0 ppm.
But the most pleasant thing awaited us next. The skirts of the dismantled pistons were also shining with pristine cleanliness. Only the bottoms and heat belts were smoked on the pistons. The gap between the first and second compression ring was covered with a light golden patina. Everything below the second compression ring was completely clean. The piston rings themselves moved freely under their own weight.
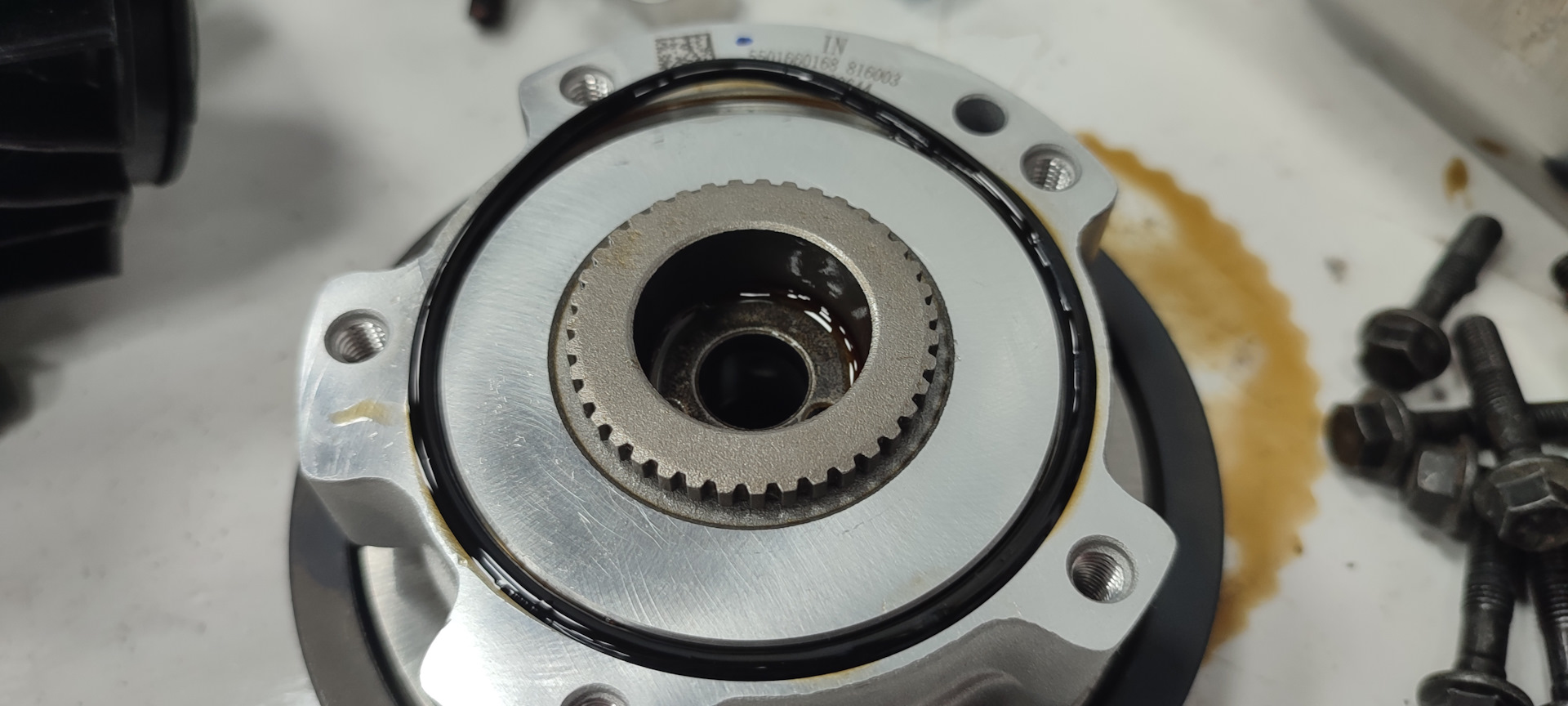
The phase shifter o-ring has slightly increased in size.
In the process of engine disassembly we had an opportunity to assess the condition of rubber products. All glands and sealants that were in contact with oil remained in pristine condition. Only the rubbers sealing the phase shifter housing have slightly increased in size. However, ASTM allows this for this type of rubber products.
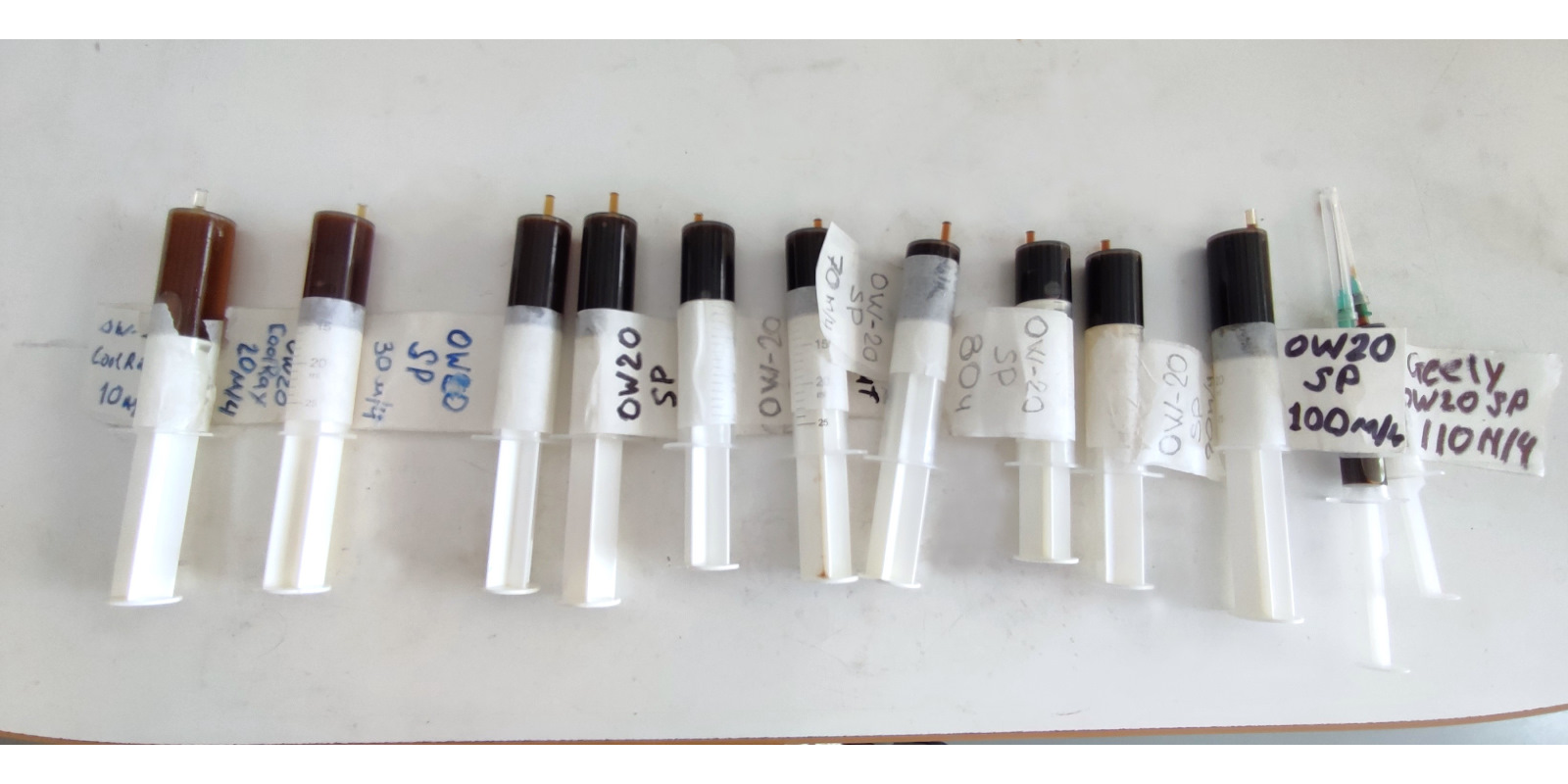
Oil samples were taken every 10 hours.
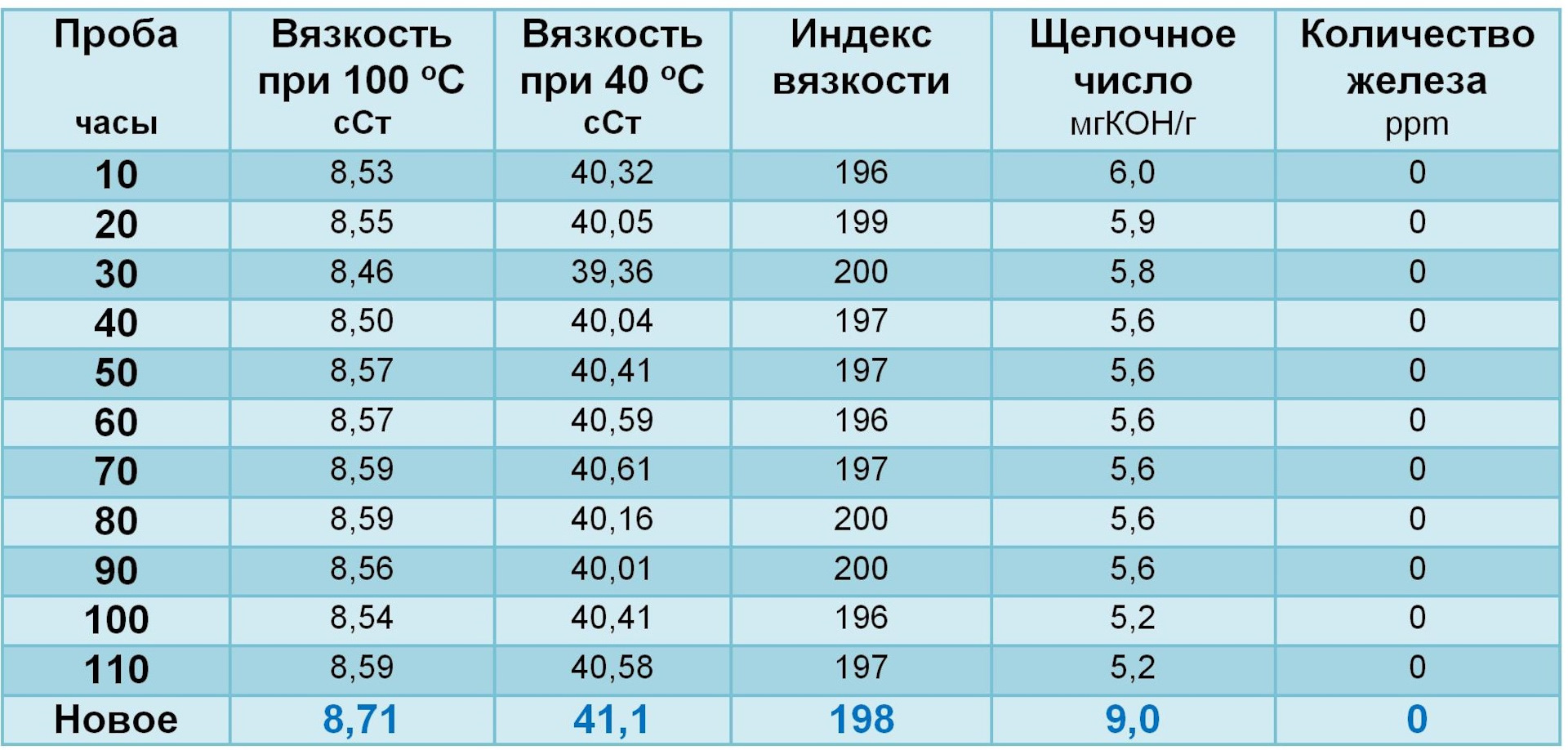
Table of VMPAVTO 0W-20 SP oil sampling results.
This is how one of our oil tests goes. The engine will soon be assembled and the tests will continue. By the way, along with the engine oil, during this test we also tested our new oil for robotized boxes. But that is another story. Keep an eye on the publications.